Production Technology, Vol 2: A Treatise of Industrial Practices
ISBN: 9788126571260
516 pages
eBook also available for institutional users
For more information write to us at: acadmktg@wiley.com
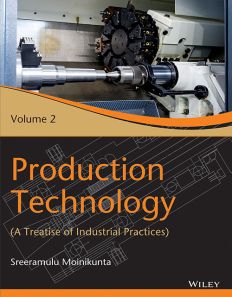
Description
Production Technology (Vol. II) is a ready reckoner data handbook for the practicing engineers and technicians in the manufacturing engineering industry. It aims to re-orient the students or the just-passed-out graduates and develop in them the skills required for the industry as a whole, in particular, for the manufacturing engineering industry. It gives reference or guidance data in the form of figures, tables and photos. This book intends to be readily referred as a reference guide for all relevant subjects with appropriate application knowledge, which is specified in design practices. The book is designed to provide the students an industry-compatible education.
Foreword
Preface
About the Author
Acknowledgments
Chapter 1: Theory of Metal Cutting
1.1 Introduction
1.2 Theory of Metal Cutting
1.3 Mechanics of Chip Formation
1.4 Built-Up Edge Formation (BUE)
1.5 Chip Breakers
1.6 Orthogonal Metal Cutting
1.7 Merchant’s Circle Diagram and its Use
1.8 Temperature in Metal Cutting
Chapter 2: Cutting Tool Technology
2.1 Introduction
2.2 Cutting Tool Materials
2.3 Tool Wear
2.4 Mechanics of Cutting Tool Wear/Types of Tool Wears
2.5 Geometry of Tool Wear
2.6 Tool Life
2.7 Machinability
2.8 Cutting Conditions
2.9 Cutting Fluids
2.10 Designing and Manufacturing of Cutting Tools
Chapter 3: Machining Processes and Machine Tools
3.1 Introduction
3.2 Turning Process
3.3 Turning Machines
3.4 Milling Process
3.5 Drilling and Boring
3.6 Drilling and Boring Machines
3.7 Planing
3.8 Planing Machine
3.9 Slotting
3.10 Broaching
3.11 Gear Cutting
Chapter 4: Abrasive Machining Processes
4.1 Introduction
4.2 Characteristics of Grinding Wheels
4.3 Types of Grinding Wheels
4.4 Types of Grinding Operations
4.5 Types of Grinding Machines
4.6 Abrasive Wheel Bonds and Cutting Speeds
4.7 Grinding Wheel Wear
4.8 Dressing and Trueing
Chapter 5: Superfinishing Processes
5.1 Introduction
5.2 Honing Process
5.3 Lapping Methods
5.4 Superfinishing Process
5.5 Polishing
5.6 Buffing
5.7 Burnishing
Chapter 6: Unconventional Machining Processes
6.1 Introduction
6.2 Characteristics of UCM Processes
6.3 Chemical Machining
6.4 Photochemical Machining
6.5 Electrochemical Machining
6.6 Electrochemical Grinding
6.7 Electrical Discharge Machining
6.8 Wire-Cut EDM
6.9 Electron Beam Machining
6.10 Plasma Arc Machining
6.11 Laser Beam Machining
6.12 Ultrasonic Machining
6.13 Abrasive Jet Machining
6.14 Water Jet Machining
6.15 Abrasive Water Jet Machining
Chapter 7: Engineering Materials
7.1 Introduction
7.2 Steels
7.3 Cast Iron
7.4 Non-Ferrous Materials
7.5 Non-Metallic Engineering Materials
Chapter 8: Phase Transformations
8.1 Introduction
8.2 Phase Transformations
8.3 Terminology
8.4 Iron–Carbon Phase Diagram
8.5 Some Conclusions
8.6 Phase Transformations: Kinetics
8.7 Isothermal Transformation (Ttt) Diagrams
Chapter 9: Heat Treatment Processes
9.1 Introduction
9.2 Types of Heat Treatment Processes
9.3 Objective-Based Categorization of Heat Treatment Processes
9.4 Annealing Processes
9.5 Hardening
9.6 Induction Hardening
9.7 Carburizing
9.8 Case Hardening
9.9 Flame Hardening
9.10 Plasma Nitriding
9.11 Tempering
Chapter 10: Surface Treatments
10.1 Introduction
10.2 Main Classification
10.3 Treatments Covering Surfaces
10.4 Treatment Altering the Surfaces
Chapter 11: Design for Manufacturing
11.1 Introduction
11.2 Design Practices
11.3 Projections
11.4 Dimensioning
11.5 Geometrical Accuracies
11.6 Introduction to Computer-Aided Design and Drafting (CADD)
11.7 Design Analysis
Chapter 12: Limits, Fits, and Tolerances
12.1 Introduction
12.2 Limits, Fits, and Tolerances
12.4 Fundamental Deviation (Allowance)
12.5 Process Allowance
12.6 Size Designations in Tolerancing
12.7 Fits
12.8 Symbols Used in Fits and Tolerances
12.9 Preferred Fits
12.10 Machining Process Capability and it Grades
12.11 Tolerance and Capability Studies
12.12 Process Control Charts
Chapter 13: Surface Finish
Learning Objectives
13.1 Introduction
13.2 Components of Surface Texture
13.3 Main Components of Surface Deviations
13.4 Measuring Parameters As Per Din En Iso 4287-1998
13.5 Surface Finish Measurements
13.6 Manufacturing Process Capability and Achievable Surface Finish
Chapter 14: Process Planning and CAPP_335
14.1 Introduction
14.2 Basic Functions of Process Planner
14.3 Manufacturing Process Planning
14.4 Review and Control Process
14.5 Introduction to Computer-Aided Process Planning (Capp)
Chapter 15: Jigs and Fixtures
15.1 Introduction
15.2 Principles of Location
15.3 Principles of Guiding Elements
15.4 Drill Jigs
15.5 Fixtures
15.6 Power Clamping Systems
15.7 Modular Fixturing System
Chapter 16: CNC Machine Tools
16.1 Introduction
16.2 What is Numerical Control Machine?
16.3 What is CNC Machine?
16.4 Introduction to DNC
16.5 Basic Principles of CNC Machines
16.6 CNC Machine Advantages Over Nc Machine
16.7 How CNC Machine Works
16.8 Application of CNC Machines
16.9 CNC Machines
16.10 Special Attachments on CNC Machine Tools
16.11 CNC Programming
16.12 Computer-Aided Design and Computer-Aided Manufacturing
16.13 Modular Tooling Systems
16.14 Tool Pre-Setting
Chapter 17: Standardization
17.1 Introduction
17.2 Design Standards
17.3 M-Material Standards
17.4 Tooling
Review Questions
Objective-Type Question
Short Answer Questions
Long Answering Questions
GATE Model Questions
Answers
References
Index